There are many types of technology involved in the electronics industry and positive photoresist technology has been some of the most important examples for many years now. Semiconductor manufacturing has evolved constantly, which has meant there has been a need for finer resolution, increased processing efficiency and greater material stability. These demands have been met by the changes in positive photoresists, which have also focused on things like environmental sustainability and the introduction of some new materials. In this article, we take a look at some of the key developments in positive photoresist technology and what it means for the electronics industry.
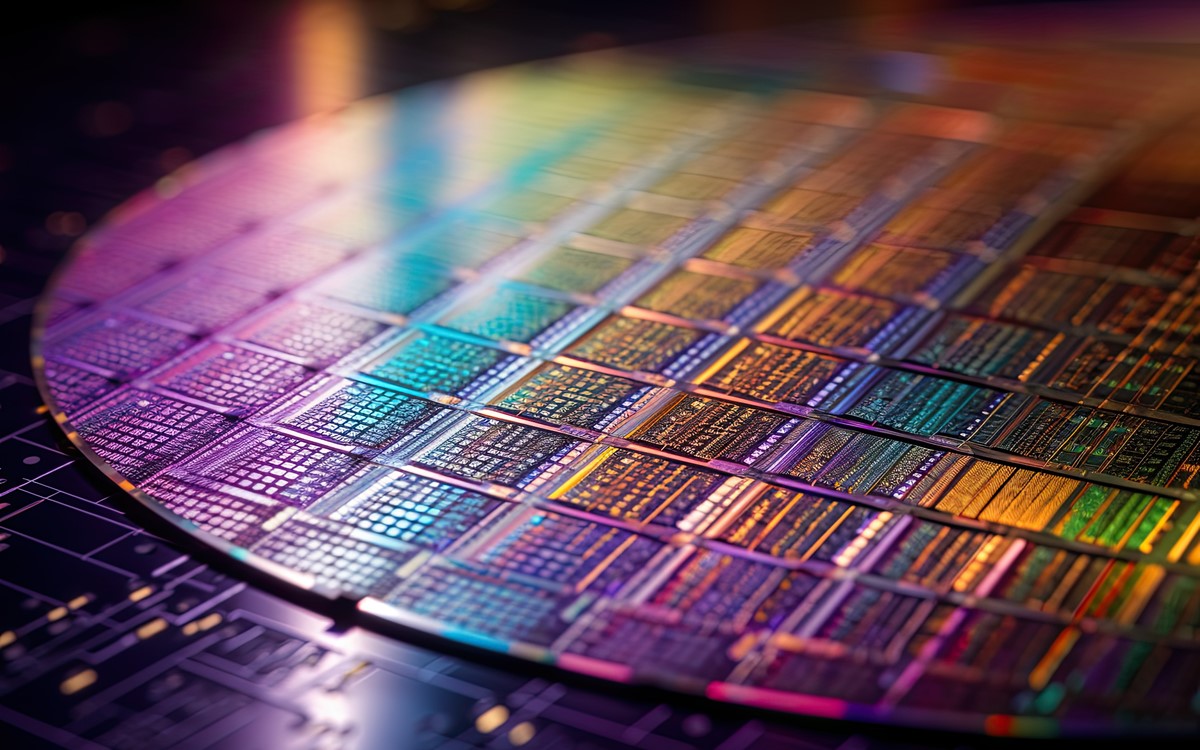
Enhanced resolution and patterning capabilities
One of the most important changes in positive photoresist technology has been the way that resolution and patterning capabilities have been improved. Increasing demand for smaller and more complex devices has meant that finer-sized features on semiconductor chips are also needed, and this is where positive photoresists come in.
There has been a significant shift towards enhancing the lithographic performance of photoresists, thanks to new formulations that are capable of responding more precisely to deep ultraviolet (DUV) and extreme ultraviolet (EUV) lithography processes. By being able to use EUV light with shorter wavelengths, it is possible to create more accurate patterning of smaller features.
By achieving finer resolution, it is possible to directly impact the semiconductor industry's capability when it comes to producing smaller, faster and more efficient devices. Cutting-edge technologies such as artificial intelligence, 5G networks and the Internet of Things (IoT) can also continue to grow, and improved resolution means that more powerful and energy-efficient chips can be developed.
Improved chemical and thermal stability
As part of modern semiconductor manufacturing, the devices that are produced need to be able to withstand harsh chemical processes and elevated temperatures. This means that the positive photoresists must be able to maintain their integrity under these conditions to ensure that the patterns they are there to define can remain precise throughout the entire fabrication process.
Photoresists which have enhanced chemical resistance and thermal stability, have now begun to be developed. They include new polymer formulations and additives which can improve the ability of the photoresist to withstand things like plasma etching, wet chemical development and high-temperature post-exposure bakes without any danger of compromising the resolution.
Improved chemical and thermal stability means greater flexibility can be brought into process integration. This is especially important when multiple patterning steps are required, and by reducing the risk of distortion of the pattern during fabrication, it is possible to ensure high yield rates and lower production costs. It is also the case that enhanced stability means that there are new opportunities to integrate positive photoresists into emerging manufacturing techniques, including 3D stacking or heterogeneous integration.
Faster development and processing times
Time efficiency in semiconductor manufacturing is crucial. New positive photoresist formulations have been designed to develop much quicker than before without sacrificing any performance or resolution. This is done by optimising the resist chemistry in order to respond more rapidly during the development phase. When coupled with advancements in exposure tools that enhance the speed of the overall lithography process, it means that there are shorter exposure and development times, allowing faster production cycles to meet high demands within the electronics market.
Reduced cycle times and increased production throughput therefore enhancing the profitability for many manufacturers. Industries that are reliant on rapid technological advancements can benefit from a quicker time-to-market for their new products, which can help set them apart in an increasingly competitive landscape.
Environmentally friendly formulations
Sustainability is now a growing concern for all industries. As traditional photoresist processes have often relied on hazardous chemicals and solvents, innovations have been needed to reduce their impact. This is why new environmentally friendly formulations have been developed which include less toxic solvents and lower energy inputs during processing. They are still able to meet the high-performance demands of modern semiconductor fabrication but have dramatically reduced the ecological footprint of the manufacturers.
This can be a big step for many electronics manufacturers in aligning with global efforts to reduce the environmental impact of the industry. It not only ensures that they are able to meet any regulatory requirements but also helps to strengthen their corporate sustainability credentials.
Novel materials and hybrid photoresists
The traditional photoresist materials have included things such as novolac resin-based formulations, but these have their own limitations when it comes to performance at advanced nodes. Therefore, researchers have explored new, novel materials and hybrid photoresist systems that can be put into practice. This includes combining the strengths of different materials to be able to create photoresists which have superior properties such as enhanced etch resistance, improved sensitivity and better process compatibility.
Hybrid photoresists have been designed to be able to work more efficiently with EUV lithography. They do this by addressing the challenges of line-edge roughness and pattern collapse that can occur at smaller feature sizes. Some systems even integrate inorganic components to be able to provide higher etch selectivity and thermal stability.
These new innovations mean that the potential applications for positive photoresists have expanded, particularly when it comes to advanced semiconductor nodes. They can enable the continued scaling of devices whilst still supporting the production of faster and more energy-efficient chips. The hybrid photoresists can also improve the overall robustness of the lithography process so that higher yield rates can be achieved whilst defects are reduced.
Positive photoresist technology advancements are playing a big part in driving the next wave of innovation in the electronics industry. By offering enhanced resolution and faster processing times coupled with improved stability and environmentally friendly credentials, they can enable the production of smaller, more powerful and more sustainable devices. The industry can benefit from higher yields and better quality, meaning that positive photoresists will remain a critical component in meeting the ever-increasing demands of modern semiconductor manufacturing.
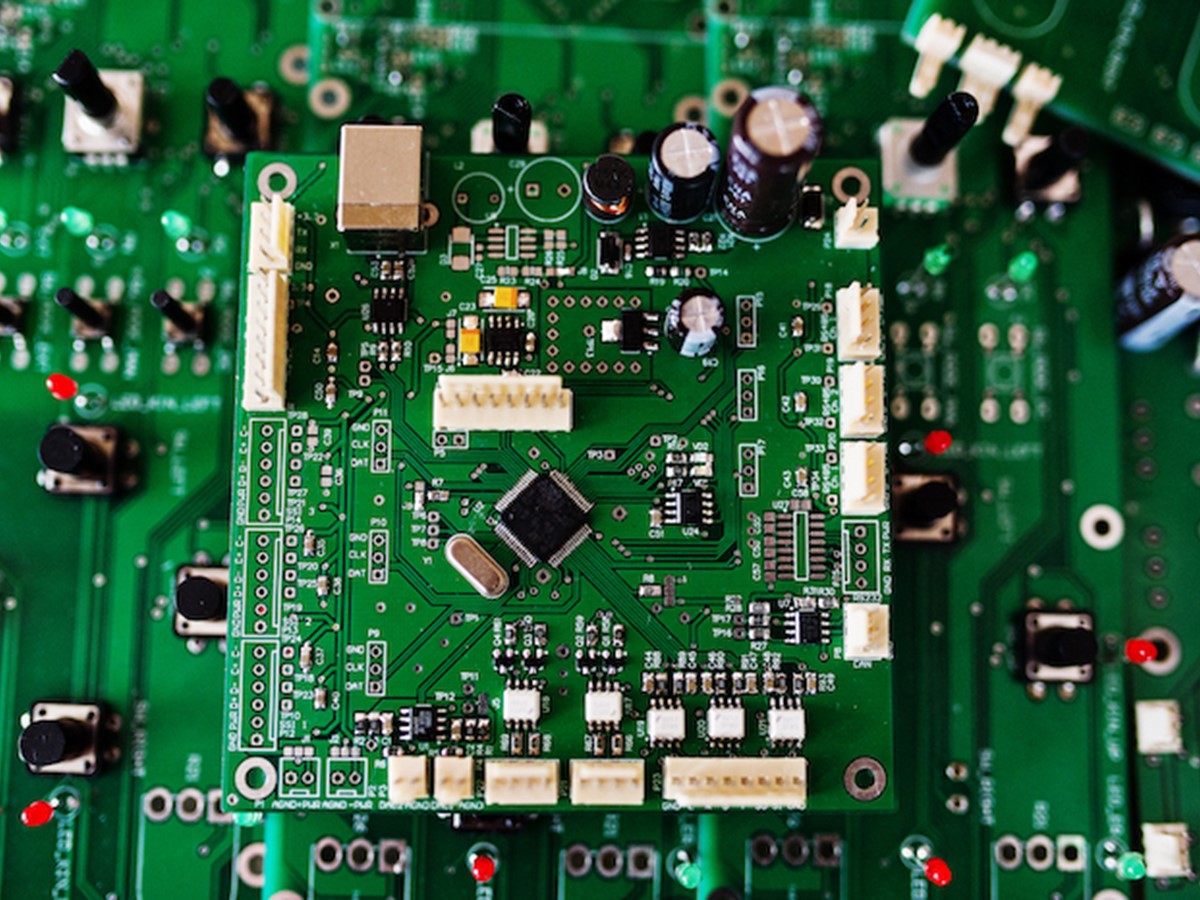